Casino Dice Craftsmanship: A Deep Dive into Modern Manufacturing Techniques
Casino dice have evolved from ancient bone and ivory artifacts to precision-engineered tools of mod…….
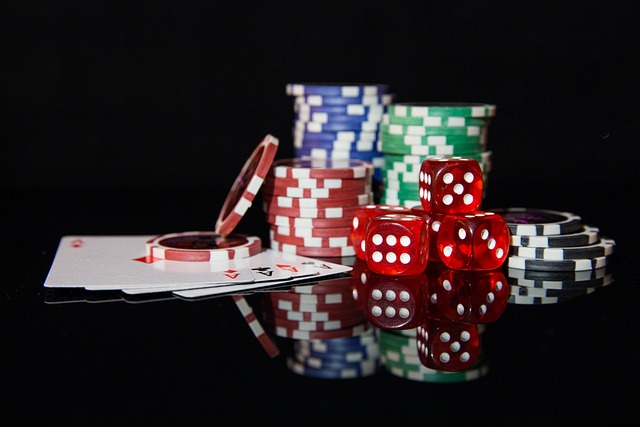
Casino dice have evolved from ancient bone and ivory artifacts to precision-engineered tools of modern casino games, crafted from high-precision plastics such as zirconia or crystalline resin. The manufacturing process is a blend of technological prowess and meticulous quality control, ensuring that each die meets stringent standards for fairness and balance. Advanced machinery like CNC milling machines and laser scanners facilitate the mass production of these dice, providing consistent and accurate results. The dies are carefully cut and shaped, followed by skilled crafting of the recognizable pips, which are crucial for the random outcome of games. Rigorous quality checks are applied throughout the process to maintain integrity and compliance with regulatory standards. Aesthetic finishing touches, including polishing and protective coatings, not only enhance the dice's appearance but also contribute to their longevity in high-use gaming environments. The production of casino dice exemplifies a commitment to excellence, combining craftsmanship, precision, and adherence to industry regulations to ensure they remain a reliable and integral part of the global casino gaming experience.
Exploring the intricate art of casino dice manufacturing, this article delves into the meticulous processes that transform raw materials into the reliable gaming tools synonymous with chance and luck. From the selection of precise materials to the precision engineering in die-cutting and shaping, each stage is critical in crafting a set of casino dice that meet both aesthetic and regulatory standards. Join us as we chart the evolution of these iconic gaming accessories and uncover the dedication to quality that ensures every roll is fair and true.
- The Evolution of Casino Dice: From Classic Gaming to Modern Manufacturing
- Material Selection and Composition: The Heart of Durable Casino Dice
- Precision Engineering: The Meticulous Process of Die-Cutting and Shaping
- Finishing Touches: Aesthetic Enhancements, Quality Control, and Regulatory Compliance in Casino Dice Production
The Evolution of Casino Dice: From Classic Gaming to Modern Manufacturing
Casino dice have a storied history that traces back to ancient times, where they were crafted from various organic materials such as bone, ivory, and even wood. Over centuries, the art of dice making evolved, transitioning from these natural substrates to more stable and consistent materials like metal alloys and finally to the high-precision plastics used today. The modern manufacturing process of casino dice is a marvel of human ingenuity and technological advancement. It begins with the selection of raw materials, which are often zirconia or crystalline resin, for their durability and ability to produce clear, random outcomes. These materials are subjected to precise molding techniques that ensure each die is perfectly cubic, with edges that meet at exactly 90 degrees. The manufacturing process also incorporates stringent quality control measures, including rigorous testing to verify that the dice are truly random, and not prone to bias or manipulation. This commitment to fairness and accuracy has made modern casino dice a cornerstone of trust in the gaming industry.
The evolution of casino dice is not just about material advancements; it also encompasses the shift from artisanal methods to mass production. Traditional hand-crafting has largely given way to automated systems, which can produce thousands of dice with consistent precision and repeatability. These modern facilities are equipped with advanced machinery, including computer numerical control (CNC) milling machines that shape the dice and laser scanning equipment that checks their surfaces for imperfections. The integration of digital technology also allows for the customization of dice, with various designs and colors available to cater to different games or casino themes. This technological sophistication has transformed casino dice from simple tools of chance into sophisticated pieces of gaming equipment that uphold the integrity and excitement of casino gaming.
Material Selection and Composition: The Heart of Durable Casino Dice
Casino dice, an indispensable component of gaming tables across the globe, are meticulously crafted to ensure fair play and durability under constant use. The selection of materials and their composition lies at the core of manufacturing high-quality casino dice. Premium cellulose acetate is often chosen for its clarity, stability, and resilience, which allows for optimal visibility of the pip or dot markings. This material, when properly processed, can withstand the rigors of repeated rolls without becoming cloudy or chipping, maintaining a consistent roll that is crucial for games like craps. The composition of the dice is carefully controlled to minimize internal stresses and reduce the likelihood of breakage. Additionally, the choice of material affects the dice’s weight distribution, which is critical for ensuring random outcomes as required by gaming regulations. Manufacturers employ advanced molding techniques to create precision-engineered dice that adhere to stringent industry standards, guaranteeing a reliable and enjoyable gaming experience.
Furthermore, the core of each die is often made from a dense, heavy material, which is encased in the outer layer of cellulose acetate. This design not only provides balance but also prevents the core from affecting the dice’s roll due to temperature fluctuations or external pressure. The balance and weight are critical factors that contribute to the dice’s performance. Each die undergoes rigorous testing to confirm its integrity and performance in a variety of conditions, ensuring that they perform consistently on the gaming floor. The dedication to material selection and composition is a testament to the craftsmanship behind casino dice manufacturing, an industry where precision and reliability are paramount.
Precision Engineering: The Meticulous Process of Die-Cutting and Shaping
In the realm of casino gaming, the integrity of each roll is underpinned by the precision engineering that goes into crafting casino dice, also known as dice. The die-cutting and shaping process is a testament to the skill and expertise required to produce these essential gaming tools. This meticulous operation begins with the design phase, where precise measurements are taken to ensure the dice adhere to stringent standards for balance, size, and fair play. The raw materials, typically a high-quality plastic or bone, are carefully cut into cubes using advanced die-cutting machines. These machines employ sharp, intricately designed dies that execute the initial shape with minimal deviation from the exact specifications.
Following the initial cutting, the dice undergo a shaping process where each face is precisely sculpted to create the distinctive pips or dots that players identify with numbers one through six. This stage is critical as it directly affects the roll of the die, ensuring randomness and fairness. Specialized tools and machines are employed here, with operators skilled in the art of fine tuning and finishing. The edges are smoothed to prevent any inconsistencies that could affect the outcome of a roll. Every step of this process is conducted under strict quality control measures to guarantee the highest level of accuracy and consistency for each die produced, thereby upholding the integrity of casino games worldwide.
Finishing Touches: Aesthetic Enhancements, Quality Control, and Regulatory Compliance in Casino Dice Production
In the meticulous process of casino dice manufacturing, the finishing touches are as critical as the raw material selection and precision engineering that precede them. Aesthetic enhancements play a pivotal role in the final product’s presentation, with each die undergoing careful treatment to ensure visual consistency and appeal. This involves polishing the die to a smooth finish, applying a protective coating, and sometimes incorporating distinctive markings or colors that align with the casino’s branding or the game’s requirements. These enhancements not only elevate the dice’s aesthetic but also contribute to their longevity, ensuring they can endure the rigors of continuous play.
Quality control is an integral aspect of the production process, encompassing a series of checks and balances to guarantee each die meets stringent standards for accuracy and fairness. This includes rigorous testing for balance and precision, as well as inspection against any deformities or imperfections that could skew outcomes. Regulatory compliance is also paramount; manufacturers must adhere to the regulations set forth by gaming authorities to ensure that the dice are truly random and do not lend themselves to manipulation. This commitment to quality and integrity is a cornerstone of trust in casino games, making the dice a reliable component of the gaming experience. Casino dice, therefore, embody the culmination of skilled craftsmanship, unwavering attention to detail, and adherence to regulatory mandates, all of which contribute to their reputation as essential tools in the world of casino gaming.