Mastering the Art and Science of Modern Casino Dice Manufacture
Casino dice have undergone a dramatic transformation from historical artifacts handcrafted from bon…….
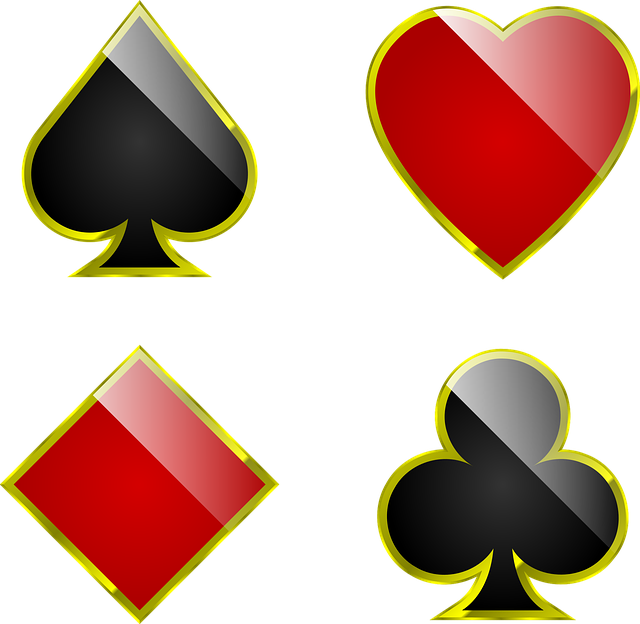
Casino dice have undergone a dramatic transformation from historical artifacts handcrafted from bones or ivory to modern precision-engineered tools for games like craps and roulette. The evolution is marked by a shift from traditional craftsmanship to advanced technology and materials science, with contemporary production relying on high-precision machinery and special polymers that offer durability and resistance to environmental factors while replicating the weight of antique dice. This modernization has standardized the gaming experience globally, ensuring fairness and random outcomes through consistent and accurate dice. The use of materials like acrylonitrile butadiene styrene (ABS) provides the necessary strength and flexibility, with techniques like injection molding, cutting, and chemical treatments ensuring each die rolls uniformly. For online gaming platforms, digital representations of dice must accurately simulate real-world physics, which is achieved through these rigorous manufacturing standards. High-quality gemstones like crystal or quartz are also used for their consistent properties and tamper-resistance, with precise engineering techniques to maintain exact tolerances and ensure fairness by eliminating potential biases. The dice undergo extensive testing to confirm they behave as mathematically expected, upholding the integrity of casino games. The production process is a testament to the commitment to quality, involving high-impact resin, CNC machining, and stringent quality control measures to meet industry standards and ensure players trust in the fairness and reliability of the dice in casino gaming environments around the world.
Casino gaming’s quintessential element, the dice, holds a fascinating journey from artisanal craftsmanship to sophisticated precision engineering. This article delves into the meticulous manufacturing process of these integral tools of chance, emphasizing the critical aspects of material selection, design for fairness, and rigorous quality control that contribute to the reliability and randomness required in casino dice. From the molding techniques shaping their physical form to the stringent tests ensuring consistency, understanding the intricacies behind each step underscores the commitment to uphold the integrity of casino games.
- The Evolution of Casino Dice: From Handcrafted to Precision-Engineered
- Material Selection and Composition: The Foundation of Quality Dice
- Designing for Fairness and Randomness in Casino Dice Manufacturing
- The Molding Process: Crafting the Physical Form of Gaming Dice
- Quality Control and Testing: Ensuring Consistency and Integrity in Casino Dice Production
The Evolution of Casino Dice: From Handcrafted to Precision-Engineered
Casino dice, integral to games like craps and roulette, have undergone a remarkable transformation from handcrafted artifacts to precision-engineered pieces of gaming equipment. Historically, dice were created by skilled artisans, often from materials such as bone or ivory, with each die being a unique creation. The process was meticulous, relying on the craftsman’s skill and eye to ensure symmetry and fairness in roll outcomes. Fast forward to the modern era, and the manufacturing of casino dice is now a sophisticated operation, driven by advancements in technology and materials science. Today’s casino dice are produced using high-precision machinery capable of creating dice with unparalleled consistency, accuracy, and quality. The materials have also evolved, with modern dice typically made from a special polymer that mimics the weight and feel of traditional dice while offering durability and resistance to environmental factors. This transition has not only standardized the dice used in casinos globally but has also enhanced the gaming experience by minimizing the potential for bias or manipulation, ensuring that each roll is as random as possible and adheres to the highest standards of fairness and integrity.
Material Selection and Composition: The Foundation of Quality Dice
Casino dice, a fundamental component of gaming houses worldwide, are crafted with meticulous attention to detail, beginning with the selection of high-quality materials. The composition and material of dice are paramount in ensuring fair play, consistency, and durability. Manufacturers predominantly use a form of plastic known as acrylonitrile butadiene styrene (ABS), which offers an optimal balance between strength and flexibility. This material is chosen for its ability to withstand the rigors of frequent use without shattering or becoming deformed, maintaining the integrity of the game. The precision of the manufacturing process is critical; each die must roll uniformly to guarantee a random outcome, which is essential in games of chance. ABS plastic, when treated with additional chemicals like acetone, can be polished to a high gloss, ensuring that players can easily read the markings. The composition also incorporates glass beads for weight distribution, counterbalancing the density of the plastic and allowing the dice to fall predictably on a flat plane, which is crucial for both land-based casinos and online gaming platforms where virtual dice are often represented by digital models that must simulate real-world physics. The dedication to quality in material selection and composition forms the bedrock upon which the reputation of casino dice is built, ensuring trust and reliability in the games they support. Advanced manufacturing techniques, including injection molding and precise cutting, combine with superior materials to produce casino dice that meet stringent industry standards for quality and performance.
Designing for Fairness and Randomness in Casino Dice Manufacturing
The manufacturing process of casino dice is a meticulous endeavor that prioritizes two critical aspects: fairness and randomness. To ensure fairness, manufacturers adhere to rigorous standards and employ precision engineering techniques. Each die is crafted from a high-quality gemstone such as crystal or quartz, chosen for its uniformity and resistance to tampering. The cutting, shaping, and polishing of these stones are conducted with specialized machinery that maintains precise tolerances, reducing the likelihood of bias in any face.
Incorporating randomness into the outcome of a die roll is essential for maintaining the integrity of casino games. This is achieved through a series of controlled steps during the manufacturing process. The dice undergo a precise drilling process to create uniform holes that are consistent across all faces, ensuring that no particular side is favored when rolled. Additionally, the edges of each face are beveled at a precise angle, which is critical for preventing the dice from coming to rest on an edge or corner during play. This beveling also smooths out the surfaces, ensuring a consistent roll every time. The final step involves rigorous testing, where dice are rolled thousands of times in controlled environments to confirm that their behavior conforms to mathematical probability. Only after passing these stringent tests are casino dice deemed suitable for use in gaming establishments. This commitment to fairness and randomness underpins the trust players place in casino games, making each roll a true test of luck.
The Molding Process: Crafting the Physical Form of Gaming Dice
The manufacturing process of casino dice is a meticulous endeavor that culminates in the creation of dice with precise dimensions and uniform density to ensure fair play and consistent rolling outcomes. At the heart of this process lies the molding phase, where raw materials are transformed into the recognizable cubes synonymous with gaming entertainment. The chosen material, typically a high-impact resin, is carefully selected for its durability and ability to mimic the weight and feel of traditional bone dice.
The molding process begins with the creation of precise molds that define the intricate shape and contours of a die. These molds are crafted using advanced technologies such as computer numerical control (CNC) machining, which ensures accuracy within micrometers. The resin is then poured into these molds, filling every contour with precision. Once set, the solidified dice are carefully extracted from their molds, revealing the initial forms of the gaming pieces. Post-molding, the dice undergo further processing to achieve a smooth, uniform surface that contributes to their aesthetic appeal and functionality. This includes sanding, buffing, and applying a protective coating to resist wear and tear during rigorous gameplay. The final product is a set of casino dice ready for deployment in gaming establishments around the world, each die a testament to the careful engineering and quality control measures that define the industry’s standards.
Quality Control and Testing: Ensuring Consistency and Integrity in Casino Dice Production
In the realm of casino gaming, the integrity and consistency of dice are paramount, as they directly impact the fairness and reliability of games like craps and other dice-based entertainment. The manufacturing process of casino dice begins with the selection of high-quality materials, typically a combination of plastic resins that ensure durability and resistance to wear and tear. These materials are meticulously shaped into the iconic six-sided form, with precision-engineered facets that guarantee a fair roll by minimizing any chance of bias.
Quality control is an integral component throughout every stage of casino dice production. From the initial design to the final product, each die undergoes rigorous testing. This includes a series of mechanical checks to verify dimensions and material composition, ensuring adherence to stringent industry standards. The dice are subjected to environmental stress tests, including temperature and humidity variations, to validate their performance under different conditions. Furthermore, randomized test rolls are conducted over numerous cycles to ascertain the uniformity of their rolling pattern. Only after passing these comprehensive evaluations do the dice meet the criteria for use in casinos worldwide, upholding the trust and confidence players place in the games they enjoy.